Er zijn veel soorten kunststofplaten met een breed scala aan toepassingen. Momenteel zijn de belangrijkste soorten polyvinylchloride, polystyreen en polyester (PET). PET-platen presteren goed en voldoen aan de nationale hygiëne-indexvereisten voor gegoten producten en internationale milieubeschermingseisen. Ze behoren tot de milieubeschermingstabel. Momenteel moeten verpakkingen voldoen aan de eisen op het gebied van milieubescherming en recycling, waardoor de vraag naar PET-vellen steeds groter wordt. Dit artikel bespreekt voornamelijk het productieproces en veelvoorkomende problemen van PET-platen.
Productietechnologie voor PET-platen:
(1) PET-vel
Net als bij andere kunststoffen hangen de eigenschappen van PET-platen nauw samen met het molecuulgewicht. Het molecuulgewicht wordt bepaald door de intrinsieke viscositeit. Hoe hoger de intrinsieke viscositeit, hoe beter de fysische en chemische eigenschappen, maar de slechte vloeibaarheid en moeilijkheid bij het vormen. Hoe lager de intrinsieke viscositeit, hoe slechter de fysische en chemische eigenschappen en slagsterkte. Daarom moet de intrinsieke viscositeit van PET-platen 0,8 dl/g-0,9 dl/g zijn.
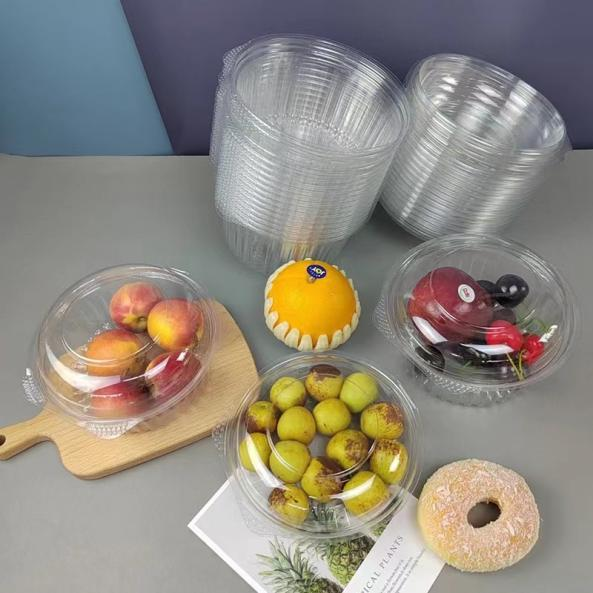
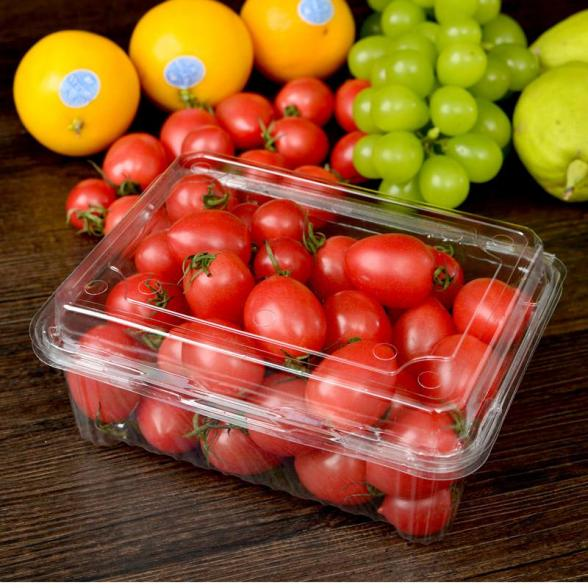
(2) Stroom van het productieproces
De belangrijksteproductieapparatuur voor PET-platenomvat kristallisatietorens, droogtorens, extruders, matrijskoppen, driewalskalanders en wikkelaars. Het productieproces bestaat uit: kristallisatie van grondstoffen, drogen, extrusie, plastificering, extrusiegieten, kalanderen en vormgeven, wikkelen van producten.
1. Kristallisatie. De PET-schijfjes worden verwarmd en gekristalliseerd in de kristallisatietoren om de moleculen uit te lijnen, en vervolgens wordt de glasovergangstemperatuur van de plakjes verhoogd om adhesie en verstopping van de trechter tijdens het droogproces te voorkomen. Kristallisatie is vaak een essentiële stap. Kristallisatie duurt 30-90 minuten en de temperatuur ligt onder 149°C.
2.Droog. Bij hoge temperaturen zal water PET hydrolyseren en afbreken, wat resulteert in een vermindering van de karakteristieke adhesie ervan, en zullen de fysische eigenschappen, vooral de slagsterkte, afnemen naarmate het molecuulgewicht afneemt. Daarom moet PET vóór het smelten en extruderen worden gedroogd om het vochtgehalte, dat minder dan 0,005% moet zijn, te verlagen. Voor het drogen wordt een ontvochtigingsdroger gebruikt. Vanwege de hygroscopiciteit van PET-materiaal zullen, wanneer water diep in het oppervlak van de plak doordringt, moleculaire bindingen worden gevormd en zal een ander deel van het water diep in de plak doordringen, waardoor het drogen moeilijk wordt. Daarom kan er geen gewone hete lucht worden gebruikt. Het dauwpunt van de hete lucht moet lager zijn dan -40°C en de hete lucht komt via een gesloten circuit de droogtrechter binnen voor continu drogen.
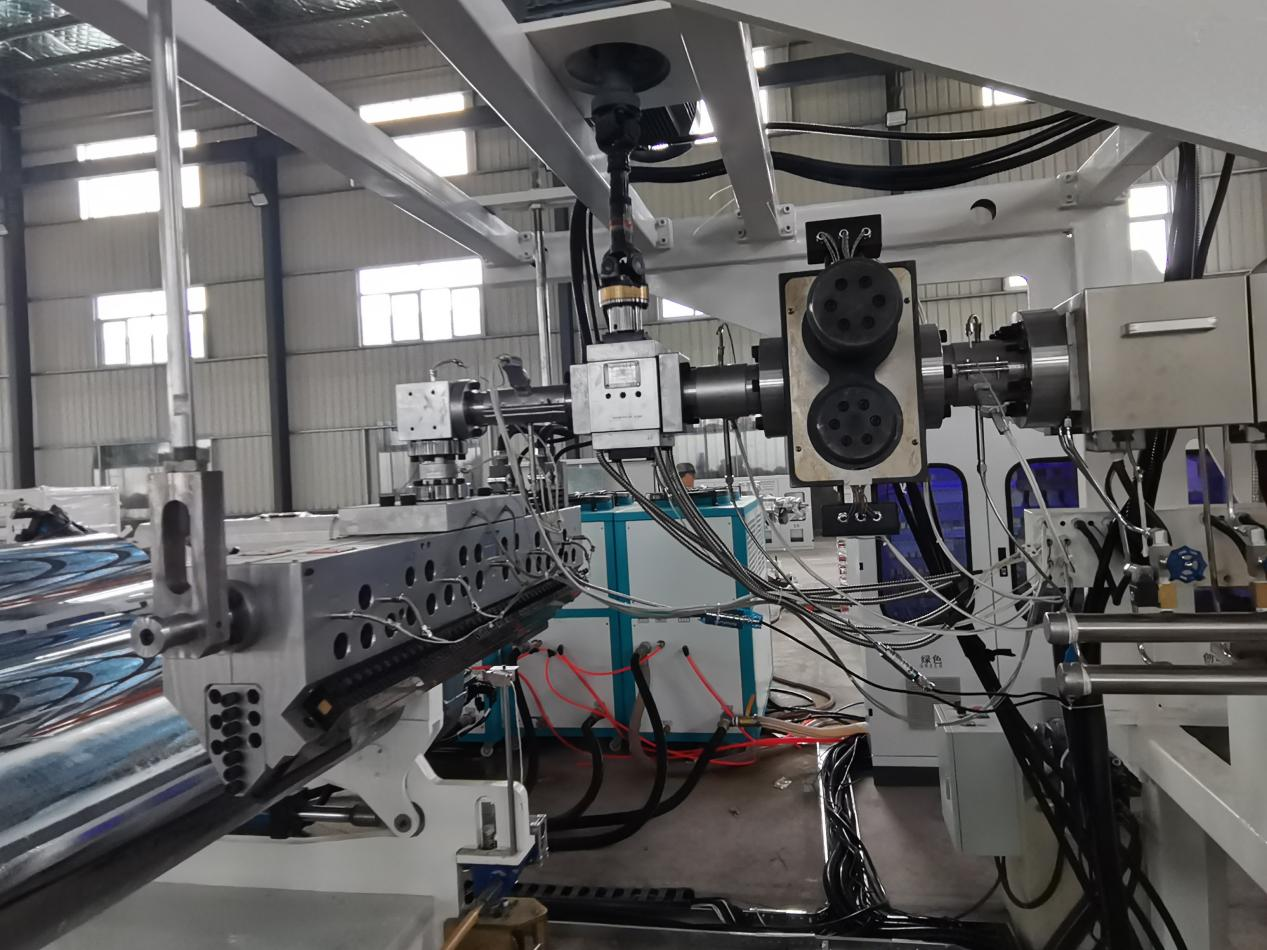
3. Knijp. Na kristallisatie en droging wordt PET omgezet in een polymeer met een duidelijk smeltpunt. De polymeervormtemperatuur is hoog en het temperatuurregelbereik is smal. Er wordt een polyesterspecifieke barrièreschroef gebruikt om niet-gesmolten deeltjes van de smelt te scheiden, wat een langer afschuifproces ondersteunt en de output van de extruder verhoogt. Keurt flexibele lipmatrijs met gestroomlijnde gasstang goed. De vormkop is taps toelopend. Gestroomlijnde lopers en krasvrije matrijslippen geven aan dat de afwerking goed moet zijn. De schimmelverwarmer heeft drainage- en reinigingsfuncties.
4. Koelen en vormgeven. Nadat de smelt uit de kop komt, gaat deze rechtstreeks naar de drierollenkalander voor kalandering en koeling. De afstand tussen de drierollenkalander en de machinekop wordt over het algemeen op ongeveer 8 cm gehouden, omdat als de afstand te groot is, het karton gemakkelijk zal doorzakken en kreuken, wat resulteert in een slechte afwerking. Bovendien zijn de warmteafvoer en koeling vanwege de lange afstand langzaam en wordt het kristal wit, wat niet bevorderlijk is voor het rollen. De kalandereenheid met drie rollen bestaat uit bovenste, middelste en onderste rollen. De as van de middelste rol is vast. Tijdens het koel- en kalanderproces bedraagt de oppervlaktetemperatuur van de wals 40°C-50C. De as van de bovenste en onderste rollen kan op en neer bewegen.
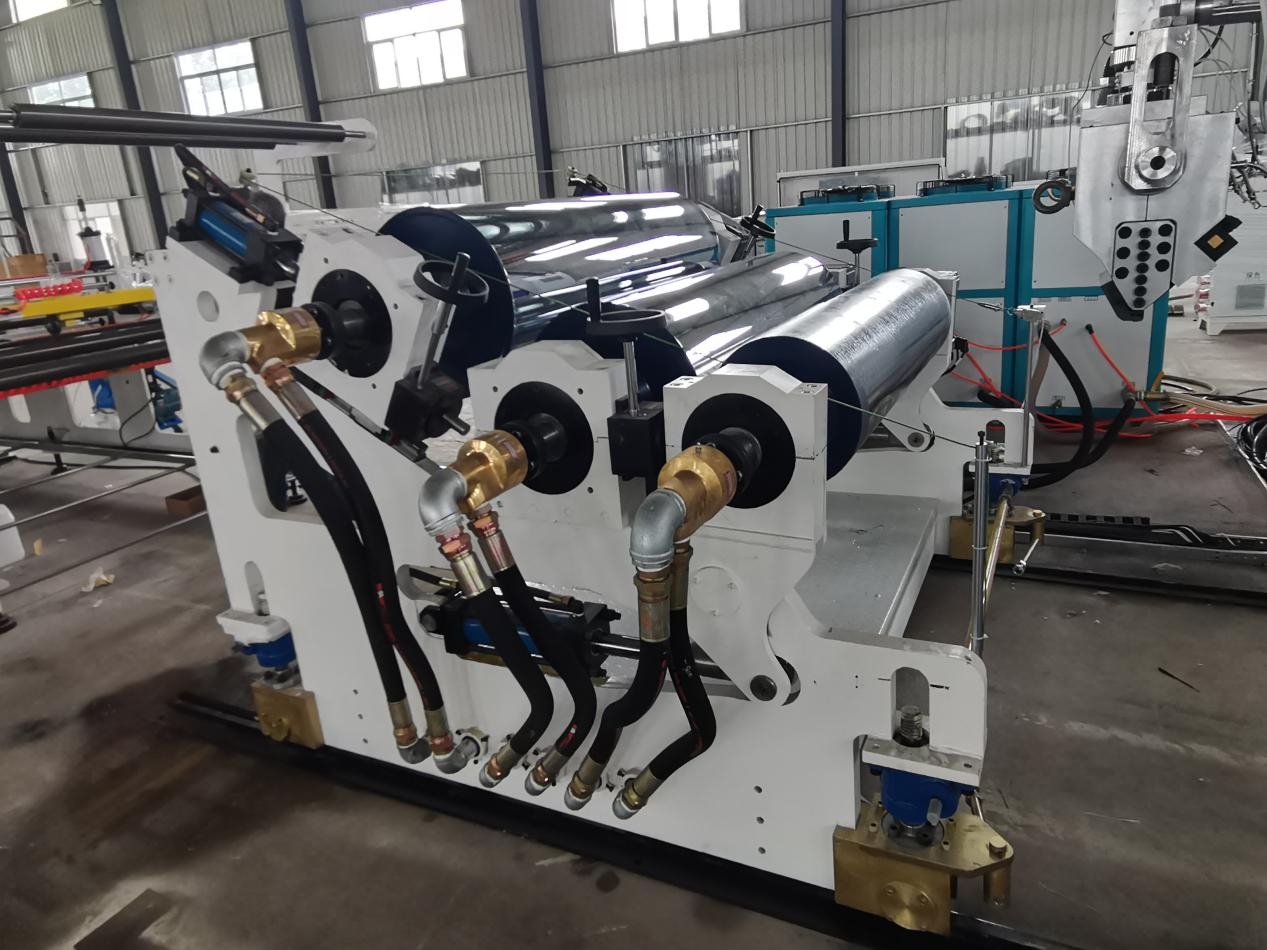
Posttijd: 28 september 2023